Material introduction
filter membrane£º (1)Ceramic membrane (2)Stainless steel filter element
0.1um Ceramic membrane
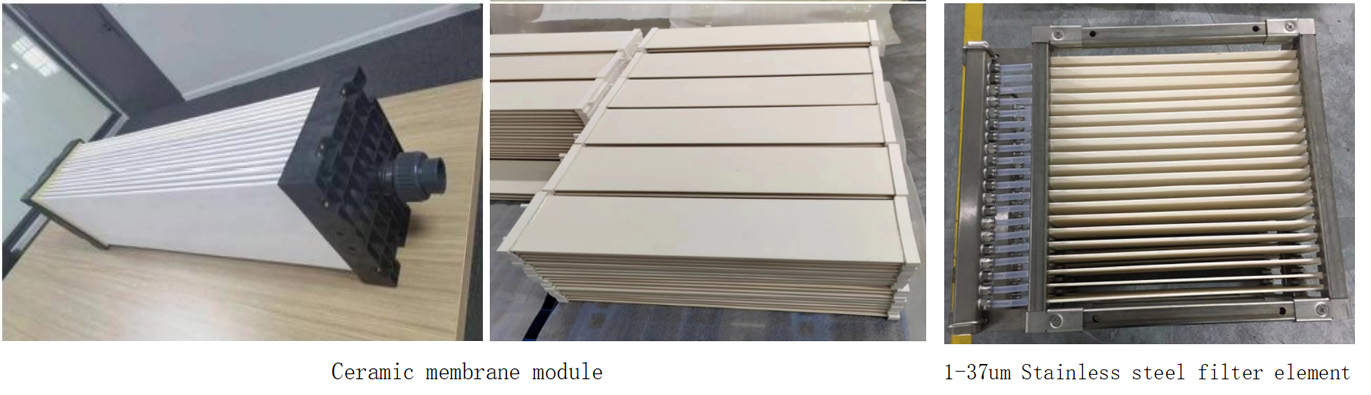
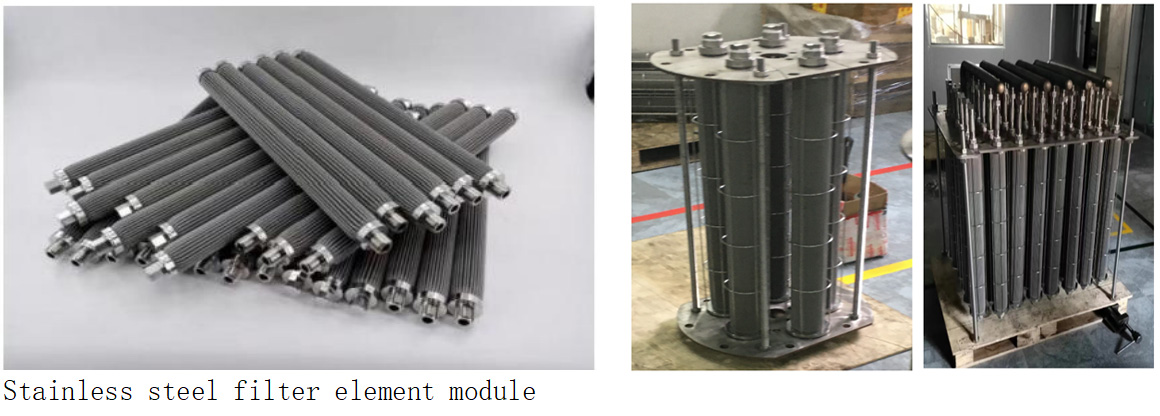
By changing the wettability of the surface of the object, that is, changing the attractive force between molecules (surface tension), the double metamaterials rely on surface tension to separate oil and water. The double superproperty of the material has a larger repulsive force on the oil molecules when compared with the water molecules. When the oil-water mixing flows throughing, the surface of the double metamaterial increases additional resistance to the oil droplets, and the water droplets flow through with lower resistance. Using this feature, it is possible to separate the difficult emulsified oil and achieve demulsification and coalescence.
£¨1£©The wetness of the continuous phase is greater than that of the dispersed phase
£¨2£©The split-phase particle size is larger than the aperture
£¨3£©Below the breakdown pressure, the dispersed phase is separated from the continuous phase
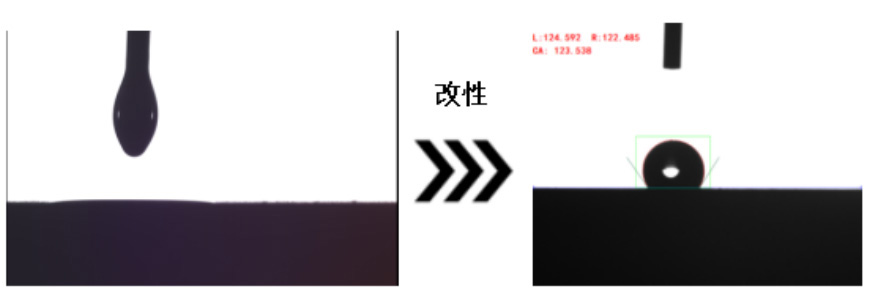
Dripping contact Angle test of hydrophilic and oleophobic coatings
(Left: Ceramic membrane , Right: hydrophilic and oleophobic coatings)
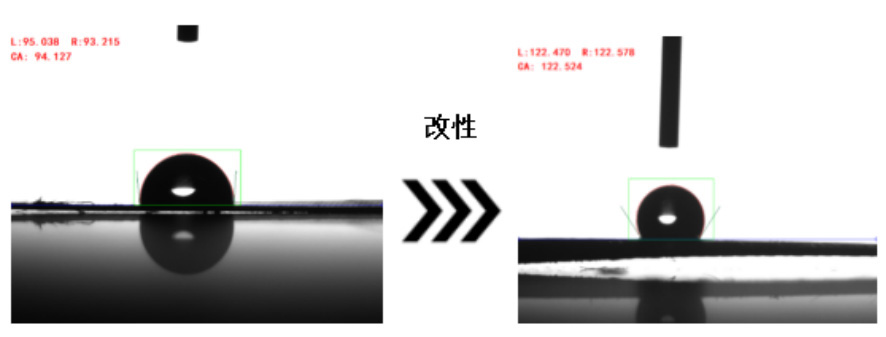
Dripping contact Angle test of hydrophilic and oleophobic coatings
(Left: Stainless steel filter element , Right: hydrophilic and oleophobic coatings)
£¨1£©Super hydrophilic and oleophobic, Super oleophilic and hydrophobic£¨2£©Greater contact Angle
(3) Greater breakdown pressure
(4) Smaller oil droplet size
(5) Less membrane usage
(6) Greater flux
(7) Higher operating film pressure
Material application
Double super swirl coalescence filtration technique£¨Operating schematic diagram£©
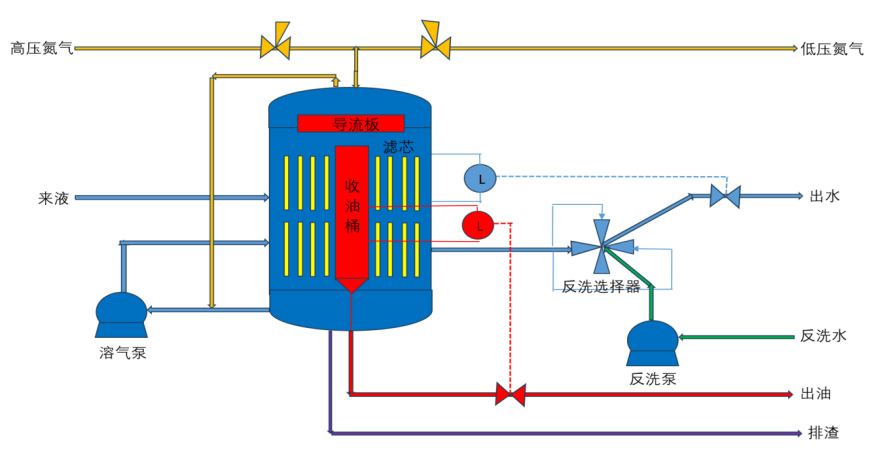
(1) Good impact resistance
(2) Oil output has low water content
(3) Full tank operation mode
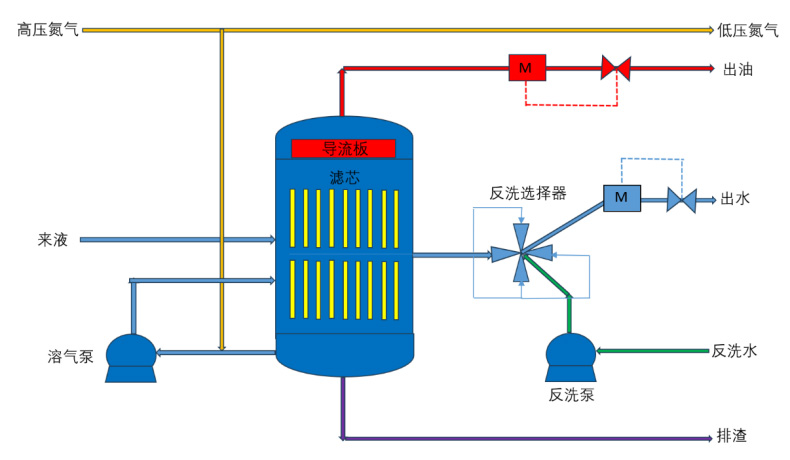
(1) Small footprint
(2) Low equipment cost
(3) Easy to operate
Schematic diagram of backwash principle
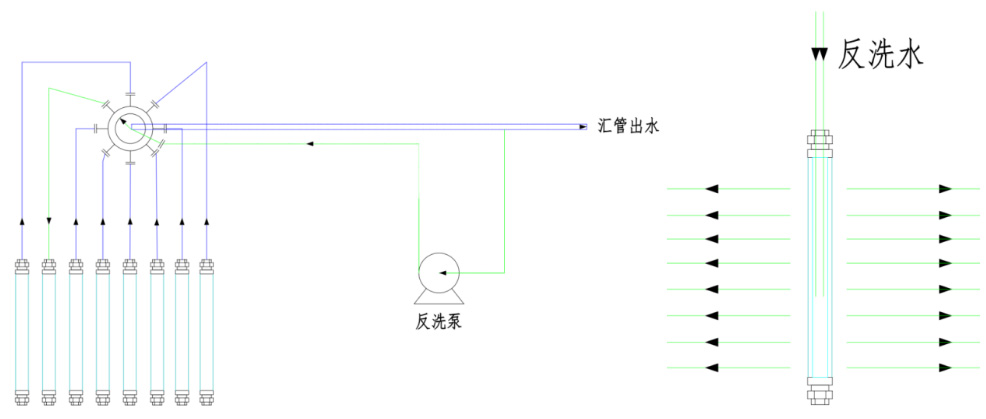
The backwash selector consists of components such as inlet branch pipe, outlet manifold pipe, frame, valve body, rotary arm, valve stem, coupling, packing, and electric controller. Mainly used for selecting branch automatic backwashing during backwashing.
The backwash selector is equipped with 8 water inlets, 1 outlet manifold, and 1 backwash inlet. When water enters, the coalescence tank is divided into 8 channels and enters the backwash selector, where the water is discharged through a manifold inside the selector; During backwashing, the inlet is rotated and the inlet branch is selected for backwashing. The backwashing time and intensity are controllable.
Dynamic structure design for cross flow microbubble cleaning, with different flow directions for gas, liquid, solid, and filtration, as shown in the figure. Bubbles float upward along the filtration membrane, floats solid pollutants on the surface of the filtration membrane, slows down the clogging time of the filtration membrane, and reduces the frequency of membrane backwashing Dynamic structure design for cross flow microbubble cleaning, with different flow directions for gas, liquid, solid, and filtration, as shown in the figure. Bubbles float upward along the filtration membrane, floats solid pollutants on the surface of the filtration membrane, slows down the clogging time of the filtration membrane, and reduces the frequency of membrane backwashing
The system operates in parallel with multiple sets of coalescing filter cartridges/ceramic membranes, using air/water washing for backwashing. When backwashing the membrane modules, one group is backwashed while the other modules operate normally, achieving online backwashing of the equipment.
Process introduction:
After mixing with dissolved gas water, the water enters the tank. The oil phase and suspended solids in the wastewater are floated to the oil receiving drum under the action of microbubbles. The oil output is controlled by a liquid level gauge chain regulating valve. Some suspended solids in the water aggregate at the bottom of the tank and are discharged regularly.
A gas phase space is set on the top of the double super coalescence tank to maintain pressure and supply air to the dissolved gas pump.
The double super coalescence tank is equipped with a filter membrane group in a single tank, which is divided into 8 groups. The effluent enters the backwash selector, and 7 groups are backwashed with 1 group. After being collected, the effluent is discharged from the manifold. The tank is equipped with a liquid level gauge and a linked effluent control valve to regulate the effluent flow rate.
The water from the backwash pump is taken from the effluent of the backwash selector and used for intermittent backwashing of 8 sets of coalescence membranes. The dissolved gas pump takes water from the tank as the inlet and nitrogen as the gas source. Part of the generated dissolved gas water is used for flotation of oil droplets and suspended solids in the water, while the other part is used for positive cleaning.
Product specifications
1. Product Specifications - Filter Element
2. Product Specifications - Filter Element Assembly
3. Product specifications - Ceramic membrane
4. Product Specifications - Membrane Components